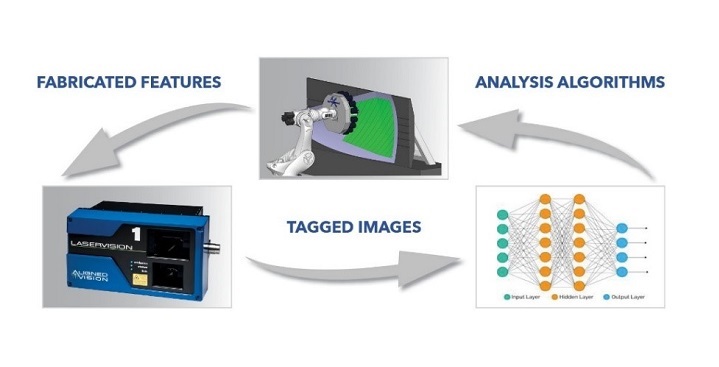
Now that artificial intelligence (AI) has reached broad commercial status in consumer and business applications, AI in manufacturing has also begun to take hold. This disruptive technology is likely to dramatically improve manufacturing operations over the next few years. Unfortunately, it is also likely that a “Driven by AI” sticker slapped on the side of a piece of equipment will become the latest version of “New and Improved.” Some instances will represent true advancements that raise quality, productivity and/or cost efficiency, but others will signify no more than a vendor’s early and unproven AI development efforts. As you explore opportunities to grow your manufacturing business through AI, how will you know which is which?
During the past five years, Aligned Vision has worked with AI quality specialists and developed some expertise of our own. We have investigated what essential elements must be in place for applications of AI in manufacturing to be fully implemented. Our specific use case, of course, is AI inspection applications with our LASERVISION large-field automatic inspection system. AI-driven LASERVISION is already benefiting some major aerospace manufacturers in production applications. Here is what we’ve learned from this experience.
Using design and engineering data
The whole point of AI in manufacturing is to find better, faster ways to physically produce the products you’ve designed, using the processes you’ve engineered. Within this framework, AI quality applications provide better, faster verification that the as-built product accurately embodies the as-designed, as-planned product. This requires much more than simple access to CAD/CAM data. AI inspection systems must be capable of importing and using CAD/CAM data.
To verify that a work-in-progress (WIP) is built as designed, an AI inspection system must be able to use CAD/CAM data to:
- Translate a virtual representation into actual attributes on the physical WIP, such as material position, fiber orientation, or the presence and location of a bolt
- Locate those attributes within the 3D coordinate system of the factory floor or work cell
- Capture those attributes in a way that allows automatic comparison to the CAD/CAM data – both what should be present and what should not, like foreign object debris (FOD)
One of the key advantages of LASERVISION automatic inspection is that it leverages our proven CAD-driven optical aiming system. We developed and advanced this system over decades of laser projection innovations, including error correction that eliminates any optical distortion in the projections (and now, in the captured images). It is easy to directly apply CAD/CAM data to LASERVISION’s calibrated high-magnification camera system. The functions described above, which are prerequisite to an AI quality solution, are already a proven part of LASERVISION’s repertoire.
Capturing good as-built data
“If you don’t have enough pixels, AI can’t learn.” This statement by an AI industrial expert encapsulates a key challenge for AI in manufacturing. To train an AI model, you need plenty of data that accurately characterizes your processes and products. In the case of machine vision-based inspections, the AI model must perform extensive feature recognition through statistical processing of captured images. If those images contain irrelevant or redundant information or are missing critical information, the AI-generated analysis algorithms will be inadequate.
The quality of captured inspection images is measured by (1) the fineness of details captured, measured by the number of pixels in the image per unit area of the surface being inspected; and (2) the amount of contrast between captured attributes. It’s analogous to your ability to distinguish between a 3 and an 8 on an eye chart, which depends on the fineness of details your eye captures and the contrast between the characters and the background. Your ability to identify the 3 or 8 improves if you magnify the image or if you increase the light your eye can capture.
Most people associate megapixels with camera resolution, but the key to good AI data is pixel resolution. Camera resolution tells you only about the camera, not about the optical engineering required for a high-quality machine vision system. Pixel resolution, on the other hand, measures the critical relationship between captured images and the actual, physical surface being inspected. Another way to think of pixel resolution is in terms of the pixelating effect. The higher the pixel resolution of an image, the more you can magnify the image before it pixelates.
LASERVISION achieves ultra-high pixel resolution because of the system’s optical design and engineering, including a 150 mm lens, high dynamic-range sensor and transform-driven autofocus functionality. When a standard LASERVISION unit is positioned 3 meters away from the surface to be inspected, it captures detailed images anywhere inside a 9 square meter surface, which translates to 1.5 gigapixels within the 9 square meters, or 167 megapixels per square meter.
Employing an open system
As often occurs in the development of a digital technology, AI in manufacturing initially required highly specialized resources and expertise, which made it impractical for production applications. It simply took too long and cost too much to take advantage of AI capabilities. Today, however, AI may be applied to a manufacturing operation by your production engineers and other non-specialists – as long as the AI-driven technology is built on an open platform.
Two AI-driven phases of your manufacturing quality program are best served by an open platform. First, AI enables rapid application development so that a system like LASERVISION may inspect the particular features of your specific works in progress. Aligned Vision offers a number of built-in analysis algorithms that we generated through AI, and we are equipped to generate more application-specific algorithms as required on your shop floor. You may also have in-house or third-party teams familiar with AI-based application development. Because LASERVISION is on an open platform, it is compatible with any PC-based vision software.
The second phase of your quality program that benefits from an open platform is closed-loop continuous improvement. The wealth of as-built data that LASERVISION generates is easily communicated to your enterprise software – manufacturing execution system (MES), enterprise resource planning (ERP), product lifecycle management (PLM), etc. Many such systems now feature AI deep learning capabilities, which analyze as-built data along with design and process data to develop manufacturing insights. With these insights, manufacturers identify new ways to predict and prevent manufacturing defects, speed production, simplify design, tighten allowables and reduce overdesign, advance toward zero-defect manufacturing, lower costs, or gain other competitive advantages.
Making better products faster with AI in manufacturing
Manufacturers of large, complex components or assemblies often still rely on human inspectors or rudimentary vision systems for in-process quality management. LASERVISION has been demonstrated to reduce inspection time upwards of 95% and achieve inspection reliability better than six sigma. Because LASERVISION also possesses all the prerequisite functionality for AI implementation – CAD/CAM transparency/visibility and production of good data on an open platform – manufacturers that implement LASERVISION are equipping themselves to maximize the operational benefits of AI quality. If you are interested in an online or onsite LASERVISION demonstration, please contact us today.