
When 3D laser projection first entered the manufacturing realm, laser pioneer and Aligned Vision founder Scott Blake focused specifically on creating “templates of light” for structural aerospace components made from advanced composite materials. The boost to quality and reduction in cycle time were nothing short of revolutionary in this first industrial application of 3D laser projection.
But far from being a niche technology with a narrow range of applications, 3D laser projection systems are now accelerating quality manufacturing efforts across the industrial spectrum. We hope this review of such applications will spark an innovative advancement for your shop floor. Let’s take a look.
From laser templating to assembly guidance
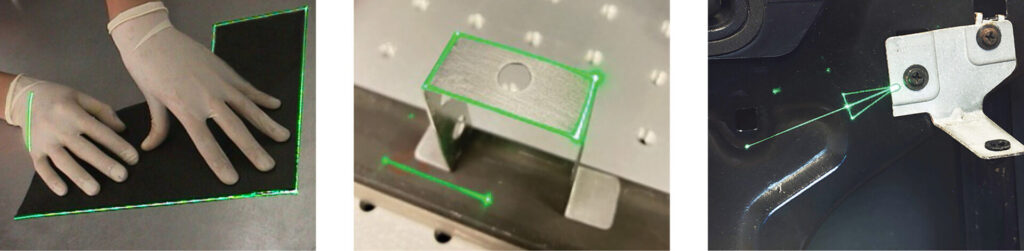
Before introducing 3D laser projection to the aerospace industry in the late 1980s, Scott had observed the current composite templating best practice, which involved physical templates made from mylar or fiberglass. These templates were painstakingly engineered and built to match specific CAD/CAM ply patterns. To build each composite component, individual templates would be pulled from the warehouse, transported to the tool, lifted and carefully aligned and affixed on the work in progress (WIP). The template’s outline would then be manually scribed. After the template was removed, the ply would be laid up.
Scribing a pattern from a template would be repeated for each ply, sometimes hundreds of times in the fabrication of one component. Not only was this practice slow and cumbersome, it was also inflexible: design changes required the manufacturer to modify or replace numerous physical templates.
Laser templating eliminated whole warehouses of physical templates. Clicking a button on a computer screen replaced the tedious process of working with physical templates hundreds of times for each build. 3D laser projection saves upwards of 85 percent on cycle time compared to the historical approach.
Scott and his team quickly realized that 3D laser projection could also boost quality and productivity in many other industrial settings. This includes both fully manual operations, like hand layup of composites, and manual procedures associated with automated systems, like positioning components for assembly. Instead of having operators translate CAD/CAM information to the 3D positioning of shop floor tools and fixtures, then taking multiple measurements before executing each manual process, 3D laser projection instantly identifies the point in 3D space where the work is to be performed:
- Hundreds of drill hole and/or fixture locations on a large structure may be identified with a laser light pattern rather than physical templates or tedious hand measurements.
- In welding, proper alignment of fixtures and components and placement of welds no longer require time-consuming interpretation of blueprints by highly skilled technicians.
- Laser guidance on a cutting table enables operators to quickly unload and kit ply patterns, even when they are cut in a complex nest to minimize scrap material.
- 3D laser projection provides digital references directly from CAD for masking and painting large structures such as aircraft or ships.
Importantly, Aligned Vision has successfully hardened LASERGUIDE 3D laser projection systems for harsh environments, such as a welding station in a shipyard or a paint hangar at an aircraft facility.
3D laser projection as a digitalization platform
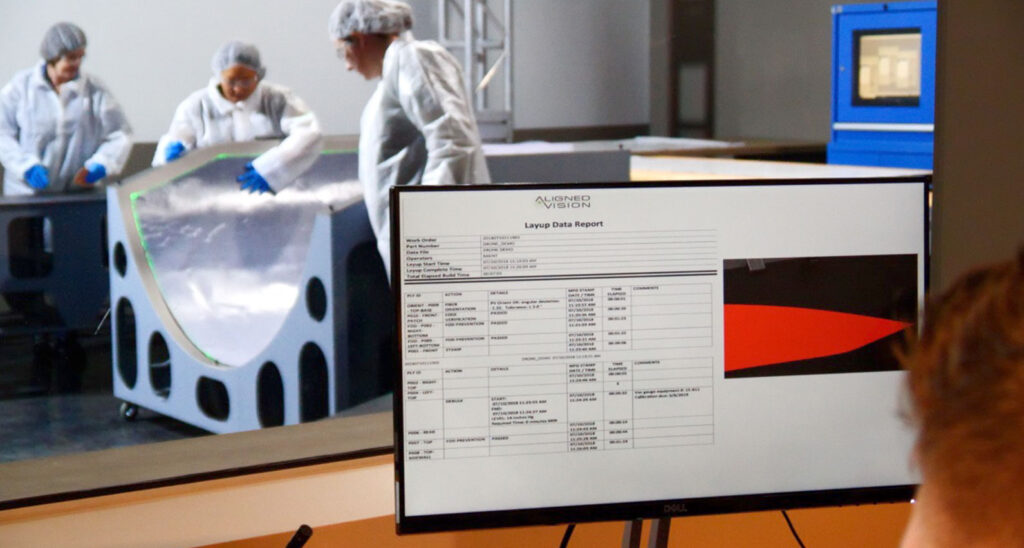
Other key Aligned Vision developments have arisen from our early recognition that the manufacturing world is going digital. Just as laser templating communicates critical manufacturing information digitally, bringing CAD data directly into the real world, so 3D laser projection systems also serve as a mature platform from which to implement other digital tools.
- Process control software enables engineers to digitally create an electronic bill of process (BOP) and electronic work instructions, including graphics, to guide correct performance of each manual task.
- Tablets or smartphone-size smart digital devices deliver manufacturing process information directly to your operators, eliminating step-away time and allowing them to remain at their workstations, adding value.
- With no new data, the CAD-driven optical aiming system of a 3D laser projection solution is able to aim a high-mag camera and capture images used in real-time automatic inspection of nearly any visible attribute on a WIP.
- Following automatic inspection, the location of any defects or suspect areas is easily pinpointed by projecting a laser pattern there.
- Each manufacturing process supported by the 3D laser projection platform is electronically documented in automatically populated reports, replacing paper travelers and documentation and helping to advance your operations to a paperless shop floor.
- Aligned Vision systems are designed to integrate projection, inspection, work instructions and data collection capabilities with enterprise resource planning (ERP), manufacturing operations management (MOM) or manufacturing execution systems (MES).
Future-proofing with a 3D laser projection system from Aligned Vision
As Industry 4.0 becomes a reality in many manufacturing facilities, new enabling technologies that further advance manufacturing quality and throughput will continue to emerge. Because Aligned Vision has designed our systems with the digital future in mind, our 3D laser projection technology will continue to support these new developments. For example, we are already applying artificial intelligence to our products. Other technologies that more directly link the manufacturing floor to the virtual realm, including virtual reality (VR), augmented reality (AR), the internet of things (IoT), edge devices and cloud capabilities, are easily combined with our laser projection, process control, automatic inspection and data delivery/collection capabilities.
Whether your digital transformation is underway or somewhere on the horizon, future-proof Aligned Vision systems will help extend your capabilities from 3D laser projection through to the digital factory and beyond. We’d love to discuss the particular needs of your shop floor with you. Sign up for an online or onsite demo today!